Повышение производительности на предприятии с помощью мониторинга оборудования
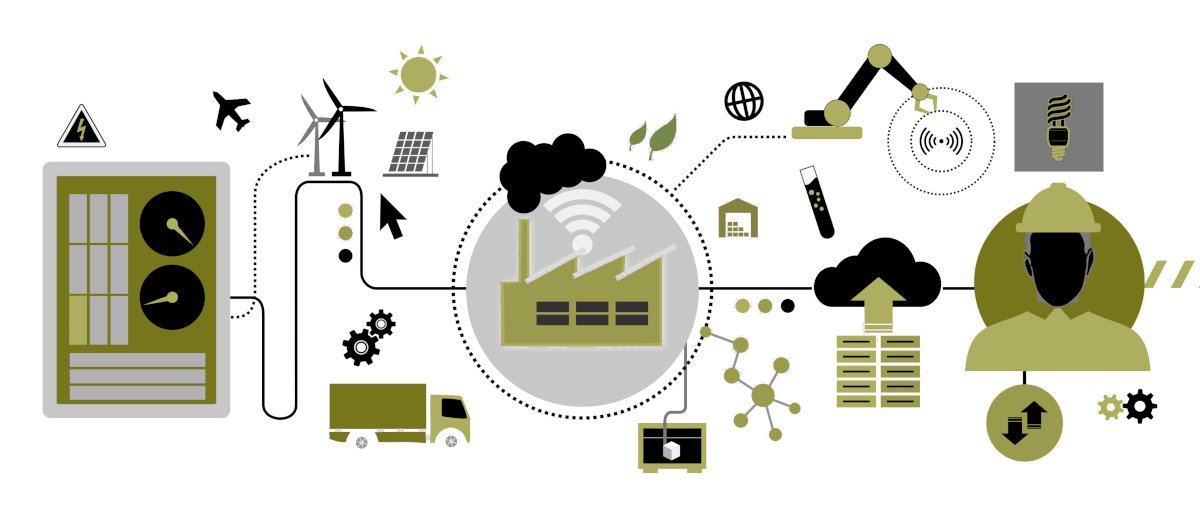
Задача повышения производительности труда на российских предприятиях стоит сейчас как никогда остро. Но достичь существенных улучшений без изменения подходов или применения новых технологий получается далеко не всегда.
Нельзя улучить то, чего нельзя измерить! По этому первой задачей при повышении производительности становится организация измерения производительности на производстве. Традиционно это делали с помощью организации хронометража и фотографии рабочего дня, на что тратилось огромное количество ресурсов, а результаты были далеко не всегда объективны.
На отечественном предприятии одно из выпускаемых изделий никак не могло достичь целевых показателей по себестоимости, чтобы стать конкурентной на рынке. Руководством было поручено провести хронометраж узкого места в производственной цепочке - токарной обработке заготовок.
Ответственный исполнитель долго искал свободное время для начала работы, а потом в течение месяца планомерно и скрупулезно делал хронометраж в сборочном цехе. Надо ли говорить, что результат был практически нулевым и установленные нормативы на операции не были существенно скорректированы. Конечно, ведь предыдущую фотографию также делал он сам.
Как же получить объективную оценку призводительности оборудования? Здесь на помощь приходят современные технологии:
- Использовать специальное программное обеспечение, уже встроенное в современные станки. Многие производители сразу встраивают в программное обеспечение своего оборудования базовые возможности получения статистики работы, которую можно использовать для оценки производительности. Некоторые шагнули дальше и дополнительно предлагают специализированные программно-аппаратные комплексы, позволяющие дистанционно оценивать состояние работы оборудования, в том числе его производительность и эффективность использования.
- Использовать информацию из лог-файлов. Если изготовитель оборудования не предлагает специальных решений для оценки производительности, то можно воспользоваться подходом, описанным в нашем проекте "Topaz": организовать самостоятельный анализ существующих лог-файлов производственного оборудования, который зачастую вместе с определенными организационными мероприятиями может дать исчерпывающую информацию о производительности и возникающих проблемах.
- Самостоятельно организовать автоматический сбор и анализ статистики работы оборудования. Значительную долю станочного парка на сегодняшний день составляют станки не оборудованные системами программного управления, где нет возможности воспользоваться подходами, описанными в предыдущих пунктах. Измерение и оценку эффективности использования такого оборудования можно организовать с помощью современных технологий, например, с помощью организации видеонаблюдения и автоматического анализа полученного изображения. Более простой в организации может быть метод измерения и оценки косвенных показателей, например, измерения тока, потребляемого оборудованием.
Большинство оборудования использует для своей работы электроэнергию, а ее потребление напрямую связано с тем, что оно делает. По этому измерив и проранжировав полученные значения, можно узнать, был ли станок включен, выполнялись ли какие-либо на нём операции и так далее.
Организовать сбор данных о потреблении тока оборудованием можно с помощью доступных на рынке микроконтроллеров и датчиков тока, а передачу данных до места сбора и обработки информации с помощью проводной или беспроводной сети. Например, очень удобно использовать для этих целей недорогие платы на базе микроконтроллера ESP8266, уже имеющих на борту модуль WiFi и аналого-цифровые преобразователи для получения сигналов от датчиков тока.
Передачу данных с микроконтроллеров в базу данных можно организовать по протоколу обмена сообщениями MQTT, упрощённому сетевой протоколу, ориентированному на обмен сообщениями между устройствами по принципу издатель-подписчик, для реализации которого существует бесплатное программное обеспечение.
Полученные значения интерпретируются в показатели производительности непосредственно в базе данных. Полученные значения могут информировать не только о статусе работы оборудования в заданный момент времени, но и с помощью алгоритмов машинного обучения оценивать повторяемость рабочих циклов оборудования, что может косвенно дать информацию о соблюдении технологии изготовления. Если рабочие циклы изготовления одной детали сильно отличается от средне-статистических или заданных технологом, то это может свидетельствовать о нарушениях технологии или проблемах с оборудованием.
Кроме информации о потребляемом токе можно также передавать информацию о положении защитных механизмов, что позволит оценивать соблюдение правил охраны труда на производстве.
Какие результаты можно получить, организовав мониторинг работы оборудования таким образом?
- Соблюдение режима рабочего дня. Если вносить в базу данных информацию о работающих операторах оборудования, то можно узнать когда каждый оператор начал работу, когда закончил, когда сделал перерыв на обед и так далее. Зачастую позднее начало или раннее окончание рабочей смены могут приводить к существенным потерям рабочего времени в течение смены.
- Выпуск продукции. Сколько на самом деле продукции было выпущено, какой такт изготовления изделий.
- Соблюдение технологии изготовления. Каждое изделие должно изготавливаться определенное время. Подготовка оборудования к работе, смена оснастки и так далее тоже должны занимать определенное время. Если это время изменилось в большую или меньшую сторону - это повод для выяснения причин таких изменений. Возможно, кто-то научился делать работу эффективнее, тогда это повод научить остальных работать также, а передовика наградить. Возможно, в работе исключили какие-либо операции чтобы повысить выработку - необходимо разобраться пока это не привело к неприятным результатам.
- Изменение профиля работы. Изготовление однотипных изделий должно приводить к фиксации одинаковых в определенных пределах изменений тока потребления. Если этот профиль сильно отличается, значит, при изготовлении продукции есть изменения, в которых нужно разобраться.
- Соблюдение требований безопасности труда. Если дополнительно к передачи данных о потреблении тока передавать данные о состоянии предусмотренных защитных механизмов (открыто,закрыто), то можно оценить выполнение операторами предусмотренных требований к охране труда.
- Исправность оборудования. Сколько остановок оборудования происходит в течение смены? Растёт ли их количество со временем? Ток потребления выше обычного? Все эти сигналы могут также заранее определить, что оборудование или оснастка требуют ремонта или замены.
Количество и тип получаемых параметров может сильно варьироваться в зависимости от исследуемого оборудования. По мере развития опыта в анализе получаемых данных, количество получаемых результатов анализа будет расширяться, предоставляя все более широкую информацию для последующего анализа производительности производства.
Важно отметить, что измерения ради измерений сами по себе не смогут привести к повышению производительности. Автоматический мониторинг и анализ результатов дает своевременную и объективную оценку текущей производительности, а также предварительную информацию о причинах её изменения.
Для менеджмента важно правильно выстроить работу с полученными результатами: их последующий анализ, разработку и реализацию корректирующих мер по снижению изменчивости процессов и повышению производительности труда (пример такого подхода описан в нашем проекте "Topaz").
Системный и систематический подход к измерению и анализу результатов повысит производительность и качество менеджмента на производстве.
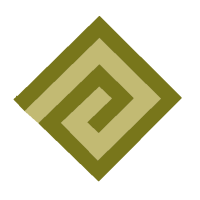
Quality managment - популярный нынче подход, часто переводят с английского языка как "менеджмент качества". Но если его перевести как "качество менеджмента" то суть подхода сразу становится понятной.
Обновлено: 18.11.2022
