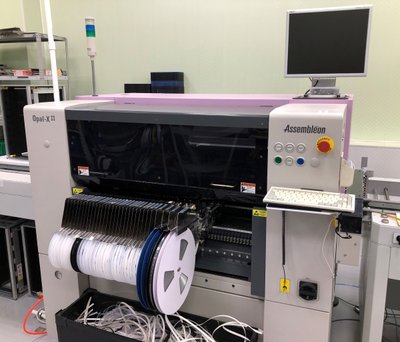
Topaz
Категория | Программы > Производство |
Статус | Архив |
Год | 2004 |
Клиенты | ЭЛАРА |
Проект был реализован уже более 15 лет назад, но опыт работы показывает, что подходы к анализу оборудования, использованные в проекте, все еще новы и не используются на предприятиях в полную силу.
Мы делимся информацией с надеждой, что использование аналогичного подхода позволит российским предприятиям самостоятельно организовать работу с лог-файлами оборудования и внедрить системный подход по работе с выявленными проблемами, тем самым повысить конкурентоспособность.
Все началось с попытки выяснить причины высокой вариабельности выпуска оборудования на линиях поверхностного монтажа в сборочном цехе. "Узким местом" сборочных линий были установщики компонентов TOPAZ. Именно они определяли производительность всех линий.
Для реализации проекта была разработана база данных MS Access, позволяющая аккумулировать данные лог-файлов с четырех линий поверхностного монтажа, анализировать их и предоставлять данные для генерации сводных таблиц в MS Excel или отчетов.
Полученная таким образом информация позволила объективно оценить реальные возможности оборудования, а также причины снижения производительности и их количественную оценку.
Лог-файл - это, как правило, текстовый файл, содержащий последовательную запись всех событий, произошедших с оборудованием. Лог-файл создается автоматически при работе оборудования.
Повышение производительности на производстве всегда комплексная задача. Она не ограничивается только его измерением. Это комплекс мероприятий по планированию, исполнению, проверке и разработке корректирующих мероприятий, известный как цикл Дёминга:
где для сборочного производства это может быть:
- Plan - это планирование:
- выпуска продукции
- технического обслуживания и ремонта
- закупки нового оборудования
- технологической подготовки производства
- обучение персонала
- режима рабочего времени
- других организационно-технических мероприятий
- Do - выполнение намеченных работ:
- выпуск продукции в течение смены,
- выполнение запланированных мероприятий,
- периодическая фотография рабочего времени
- корректировка технологических процессов
- и так далее.
- Check - проверка результатов работы:
- проверка качества выпущенной продукции
- анализ фактических финансовых и временных затрат на выпуск продукции
- анализ соблюдения технологической дисциплины
- Act - управляющие воздействия:
- разработка мероприятий по повышению производительности труда
- изменение технологических процессов
- внедрение корректирующих мероприятий в цехе.
Традиционно проверка результатов работы ограничивается проверкой качества выпускаемой продукции, оценкой выполнения плана, периодическими проверками технологической дисциплины, иногда - фотографией рабочего времени. Но эти методы не позволяют получить информацию о причинах вариабельности (изменчивости) производственного процесса. Для реализации успешного процесса повышения производительности необходим эффективный инструмент ежедневной количественной оценки производительности на сборочном производстве.
Нельзя улучшить то, что нельзя измерить!
Разработанная база данных "Topaz" предоставляет такую возможность, используя для сбора и анализа данных лог-файлы, которые автоматически создаются современным производственным оборудованием. Это позволяет и без существенных трудозатрат получать объективную количественную оценку производительности производственного оборудования по широкому кругу показателей.
Проанализированные данные из базы данных "Topaz" становятся прочным фундаментом для дальнейшего анализа мастерами, технологами и конструкторами и разработке мер по повышению производительности труда.
Лог, формируемый установщиком компонентов TOPAZ-X, представляет собой тестовый файл CURRENT.log
с информацией о работе оборудования примерно следующего содержания:
10/08/04 19:41:10 #003:PCB LOADED
10/08/04 19:41:10 ##:COMPLETED BLOCK.1
10/08/04 19:41:10 ##:PRDDATA./0/107/30163/0/107/65.5/0.0/4.6/13.0/7702540/30460/
10/08/04 19:42:18 #001:PCB COMPLETED.
10/08/04 19:42:21 #003:PCB LOADED
10/08/04 19:42:21 ##:COMPLETED BLOCK.1
10/08/04 19:42:21 ##:PRDDATA./0/108/30164/0/108/65.5/0.0/4.6/13.0/7702640/30460/
10/08/04 19:42:31 #20: FIDUCIAL ERROR.
10/08/04 19:42:31 ###E51
10/08/04 19:43:46 #001:PCB COMPLETED.
10/08/04 19:43:49 #003:PCB LOADED
10/08/04 19:43:49 ##:COMPLETED BLOCK.1
10/08/04 19:43:49 ##:PRDDATA./0/109/30165/0/109/65.5/0.0/4.6/13.0/7702740/30460/
10/08/04 19:44:57 #001:PCB COMPLETED.
По окончании каждой смены оператор линии поверхностного монтажа сохраняет лог-файл оборудования на диск и передает его сотруднику вместе с отчетом об остановках оборудования, ответственному за сбор и анализ информации.
Скрипт базы данных загружает лог-файл, анализирует его, соединяет информацию с уже имеющейся информацией в базе данных и проводит синтаксический анализ текста (парсинг).
Проанализированная информация также сохраняется в базе данных "Topaz".
Для уточнения причин каждый оператор в течении смены заполняет бумажную форму-отчет о причинах остановок, которую потом используют для уточнения данных в системе о причинах остановок. Для этого система предлагает заполнить форму, в которой указана информация о времени и длительности остановок оборудования, вычисленной на основании полученных лог-файлов.
После этого база данных сможет сформировать таблицы и отчеты с показателями работы оборудования. Условно их можно разделить на три группы:
- показатели производительности
- показатели соблюдения технологии и распорядка дня
- показатели работы с ошибками оборудования
Показатели производительности
- Коэффициент непрерывности работы - отношение времени непрерывной работы к общему рабочему времени.
- Коэффициент производительности - отношение фактического выпуска продукции к максимально возможному при непрерывной работе.
- Фактическое время сборки одной платы (максимальное, минимальное по операторам и сборочным линиям). Разница значений между операторами или изменение этого параметра во времени должно стать причиной внимательного разбора причин таких изменений. Изменение установок скорости работы - почему? Изменение управляющей программы -почему? и так далее.
- Количество фактически собранных плат по типам.
Показатели соблюдения технологии и распорядка дня
- Фактическое время начала смены. Если по трудовому распорядку первая смена начинается в 6:00, то время начала смены в базе данных принимается как первая выпущенная плата после 6:00.
- Технологическое время на подготовку оборудования к работе - это время с момента начала смены до времени выпуска первой платы. Сильное отклонение этого показателя от среднестатистического или предусмотренного технологическим процессом должно стать объектом внимания при анализе показателей и выяснения причин отклонения.
- Фактическое время окончания каждой смены - время выпуска последней платы перед окончанием установленного расписанием времени смены.
- Длительность перерывов на обед - длительное время остановки в обеденное время можно рассматривать как остановка из-за обеда оператора (ошибки в работе не устраняются быстро). Наличие такого показателя в отчете заставляет менеджмент задуматься об изменении режима работы в обеденное время, если есть несколько операторов.
- Технологическое время на перенастройку оборудования на новую программу. Здесь также важно сравнить его с требуемым по технологическому процессу и разобраться в причинах сильных отклонений.
- Технологическое время на замену питателей (катушек) с радиоэлементами. Вычисляется как период с момента появления ошибки об отсутствии радиоэлементов в питателе и временем следующей записи в лог-файле. Длительный период времени может свидетельствовать об отсутствии нужного количества радиоэлементов у оператора, из-за чего ему приходится ходить на склад за ними и так далее.
- Технологическое время на техническое обслуживание - сильное отклонение от установленного может также говорить об недостаточном объеме проведенных работ или наоборот затягивании. Важно разобраться в истинных причинах.
- Время, затраченное на ремонт оборудования в динамике за последние несколько периодов (месяцы, годы). Например, увеличение общего времени ремонтов во времени может стать сигналом для более глубокого погружения в эту тему. Нет запасных частей? Нет специалистов? Не заключены договора на сервисное обслуживание? ... и так далее.
Показатели работы с ошибками оборудования
- Статистика по типам ошибок и их причины. Здесь в лог-файлах может быть недостаточно информации об истинных причинах возникновения ошибок в работе. Для уточнения причин остановок в работе были внедрены специальные сменные отчеты по ошибкам , где операторы были обязаны уточнять причины длительных (более 5 минут) остановок оборудования.
- Время реагирования оператора на возникающие ошибки и длительность их устранения
- Полнота заполнения сменного отчета по ошибкам оператором - все ли длительные остановки были отражены в отчете.
Полученные и предварительно проанализированные данные могут быть импортированы в сводную таблицу MS Excel для дальнейшего глубокого анализа данных в составе сводной команды из мастеров, конструкторов, технологов, сметчиков и начальника цеха.
Команда должна определить наиболее существенные причины, влияющие на производительность работы. Специалисты должны разработать корректирующие мероприятия для снижения влияния или устранения выявленных проблем, внести изменения в планирование и распределение ресурсов.
Входные данные для разработки корректирующих мероприятий может выглядеть следующим образом:
По результатам работы за неделю формируется отчет, содержащий информацию о текущей производительности, причинах и времени остановок, а также изменение параметров в динамике за несколько предшествующих отчетных периодов.
Анализ полученных данных и разработка корректирующих мероприятий являются самыми важными в организуемом процессе повышения производительности, а регулярное их выполнение - залогом успешного внедрения процесса.
При системном подходе к получению информации об эффективности работы многие и многие проблемы становятся видимыми. Большая часть проблем может быть решена быстро и без финансовых затрат, только изменением организации работ на производстве, в снабжении, внесением правок в технологические процессы или управляющие программы.
Например, простое информирование сотрудников о достигнутых ими показателях на общей доске объявлений позволило в среднем увеличить операторов производительность на 10-15 %! Здесь включается элемент соревнования между рабочими, что положительно сказывается на общей производительности труда.
Для сложных системных проблем, где решение не может быть простым, с внедрением процесса анализа лог-файлов установленного оборудования появляется хорошая база для выяснения причин их возникновения и инструмент для оценки принятых решений.
Важно отметить, что сама база данных "Topaz" и данные являются только одним инструментом для объективной оценки работы оборудования в комплексном процессе повышения производительности на сборочном предприятии. Для достижения целей повышения производительности важны каждый из этапов цикла PDCA: планирование, исполнение, проверка и корректировка.
Успех внедрения процессного подхода в ежедневную деятельность предприятия в сильной степени зависит от вовлечённости руководства, в неизменном желании его поддерживать и стимулировать работу коллектива в комплексном поиске причин снижения производительности на сборочном производстве и реализации намеченных мероприятий по улучшениям.
Каждое предприятие, имеющее у себя современное оборудование, может использовать данные лог-файлов для анализа его производительности. Для этого не нужно приобретать специальное программное обеспечение от производителя, все можно сделать самостоятельно. После того как организация научится использовать получаемую из лог-фалов информацию для повышения производительности сборочного производства, можно рассматривать приобретение дорогостоящего специального программного обеспечения.